Patented Modular Connector Technology
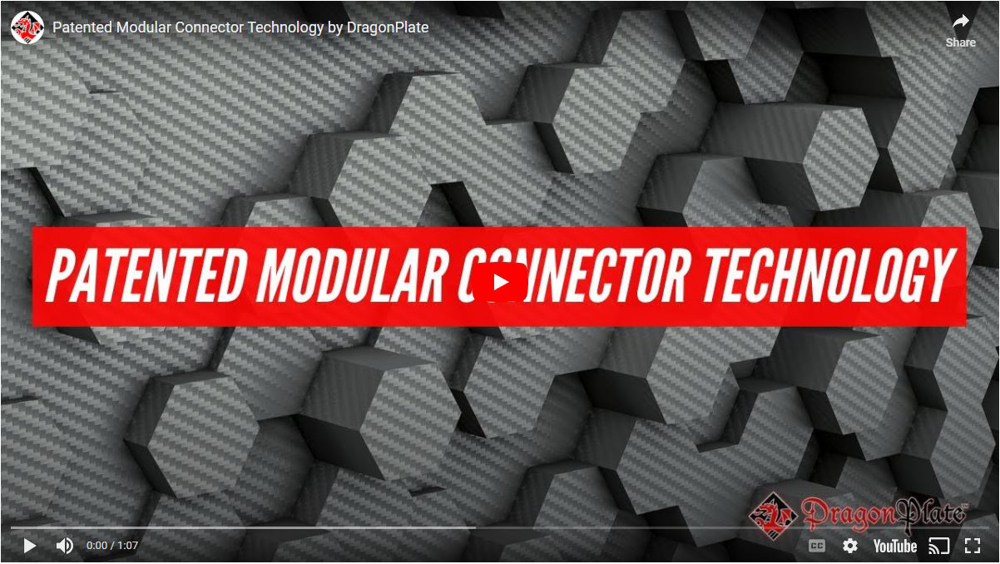
Designed specifically for building robust structures from carbon fiber tubes.
DragonPlate lightweight tube connectors provide an easy and robust method for connecting our 0.5", 0.75" or 1" roll-wrapped or braided carbon fiber tubes together to form lightweight rigid structures. Using these aluminum connectors, our carbon fiber tubes can be connected to form much longer disassembleable tubes and complex 3D structures. Both 2D and 3D joints are possible. The connectors are adhesively bonded into the ends of the carbon fiber tubes using an epoxy. We recommend Scotch-Weld 2216 adhesive. Click here to learn more about our Modular Carbon Fiber Tube Connectors.
Patent 9,803,672 B2
In addition to the basic function of the connectors, our patented design includes a ridged and slotted design that virtually eliminates metal to carbon delamination due to thermal expansion and contraction. One of the primary concerns when bonding metal fittings into carbon fiber tubes is the fact that the metal component, when subjected to reductions in temperature, will shrink much more than the carbon fiber tube. This is due to a mismatch in the thermal expansion coefficients (CTE) of the two materials, with the metal component having a CTE of over ten times that of the carbon fiber tube. As a result, delamination can occur between the aluminum insert and the carbon fiber. In addition, thermal cycling can cause fatigue problems in the joint.
As an example, for a 0.75" carbon fiber tube and aluminum fitting, the aluminum diameter may change up to 0.001” over a temperature change of only 50° F. The diameter of the carbon fiber tube, however, will reduce only about 0.0001”. As a result, the adhesive layer is put into tension, thus imparting a peel stress on the epoxy. Since the peel strength of epoxy is typically between 25 and 50 psi, even this modest contraction of the aluminum part may cause internal peel stresses to exceed these values, causing the bond to fail and the parts to delaminate from one another.
To eliminate this problem, our patented connector incorporates a slotted tubular design, which has a two-fold effect. First, the slots allow the aluminum to contract circumferentially without as much change in the nominal diameter of the insert. Secondly, the slots provide compliance to the part, which further alleviate peel stresses by prohibiting the aluminum part from imparting as much peel force on the adhesive layer. In addition, this design includes a ridged outer surface. This further strengthens the bond inside the carbon fiber tube by placing more epoxy in shear (and most structural epoxies are about 100 times stronger in shear than in peel).
This combination of form, function, and resistance to thermal delaminations makes our DragonPlate tube connectors a versatile and robust option for many projects. Each connector also comes with a foam plug to contain adhesive and enough bond line control micro glass beads to ensure a proper bond fit.